Ford announced that it has started production of the new Transit Custom at the renovated Yeniköy assembly line in Turkey, which uses advanced solar energy technology, end-to-end AI-driven management, and assembly lines that reduce noise.
With a €2 billion investment in the manufacturing facilities, the Yeniköy assembly line was developed to set a new benchmark in automobile production in Turkey and lead the electric transformation of the automotive industry in the region.
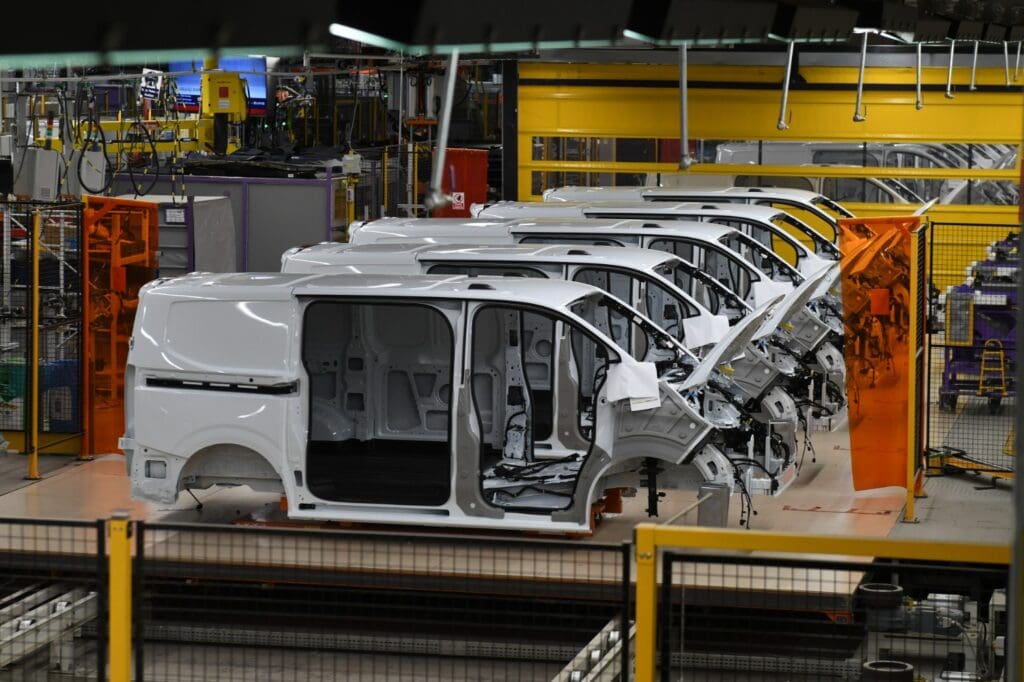
The production unit is now one of the most efficient factories in the entire automotive industry. Part of the factory’s annual electricity consumption is provided by innovative embedded applications, including the first use of photovoltaic glass walls in the Turkish automotive industry. The rooftop solar panels also contribute to reducing dependence on externally sourced electricity, all of which is certified as renewable.
In addition, Solar Wall technology captures sunlight to heat the facility’s water, reducing the use of natural gas. Furthermore, Ford clarified that cutting-edge production solutions are used throughout the production process. Real-time data and artificial intelligence combine to create virtual production simulations, helping optimize production efficiency and enabling agile responses to demand fluctuations, component supply, or variations in production processes.
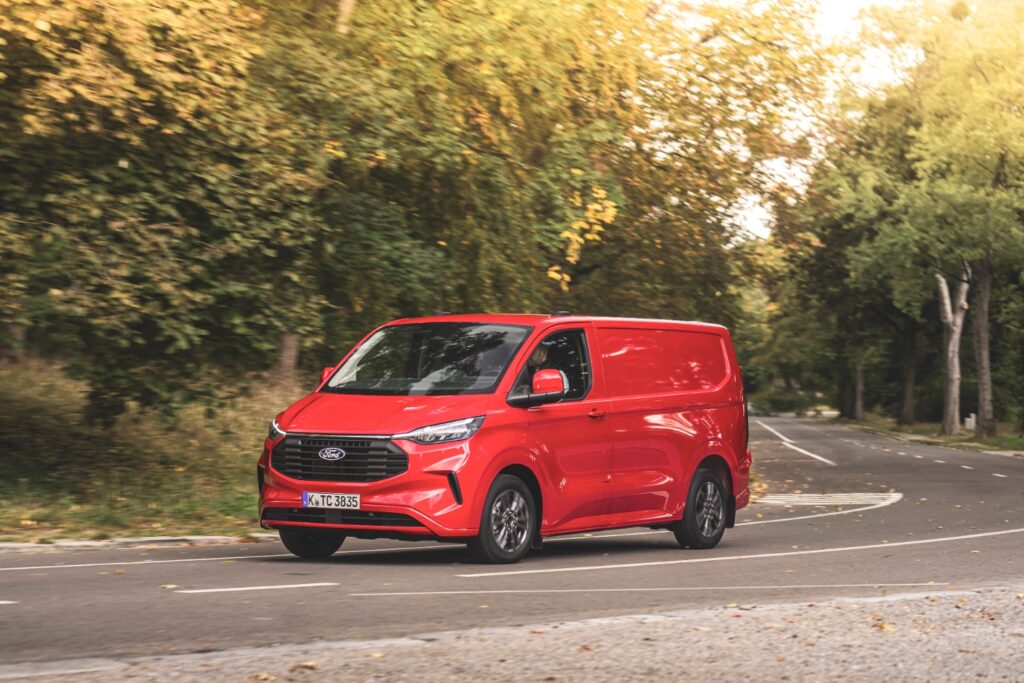
Next year, mass production of the electric E-Transit Custom and E-Tourneo Custom will begin, supported by sustainability credentials that will contribute to Ford Otosan’s assembly line in Turkey achieving carbon neutrality in all its facilities by 2030.
“The state-of-the-art Yeniköy assembly line is already contributing to Ford Pro’s improvement of the quality offered to its customers and, being one of the most efficient automotive production units in the world, it sets new standards for the production of multi-energy commercial vehicles on a large scale,” emphasized Hans Schep, General Manager of Ford Pro Europe.